You are probably already visualising your finished, marketed product. The idea of your connected object coming to life!
What could be more normal? Designing a connected object also means envisaging, in the more or less long term, its industrialization.
While the first developments may give the satisfaction of seeing a concept come to life, there is still a long way to go to get to the finished product. everal stages are necessary prior to arriving at a product that might be industry-ready.
This is what we will see here.
Why should the industrialisation phase be thought of as early as possible?
We are often far from imagining the long development and manufacturing stages required for an IoT product (for the Smart Home, for example) to end up on the shelves of a retail shop.
At least, we tend to minimise these steps!
Quite often, some technical constraints may be encountered during the development process. Why is this? Because of a lack of anticipation and precision of the desired functionalities. This problem is often encountered when developing an IoT application. Unfortunately.
In B2B or B2C, developing a connected object and marketing it is always a necessity. It is better to be prepared to launch into this “battle” and to avoid common mistakes. Mistakes that can be costly (in terms of time to market and ROI).
Why is it costly not to anticipate industrialisation sufficiently?
1. The risk of multiplying iterations
Your product will go through several iterations. This is inevitable. The design is rarely 100% right the first time! Anything prototyped in the development phase is rarely 100% representative of the production parts, and it is this discrepancy that makes these iterations necessary.
Each new loop involves additional costs and time, it’s a continuous improvement process and each iteration gets you a little closer to the perfect product.
Our advice: don’t try to use iterations to add features. The purpose of iterations is to make adjustments to the product.
2. The risk of not passing the certification tests
The industrialisation phase includes numerous series of tests. Robustness tests, waterproofing tests, climatic tests, noise tests, endurance tests and performance tests. The aim is to put your product to the test with “real” parts that are as close as possible to the final product to ensure the safety of future users.
You will also have to approach laboratories for “pre-qualifications” or even certifications if you have your final product.
If all the tests are conclusive: R.A.S.
On the other hand, if you fail these tests, especially the pre-qualification tests, the correction of your product may upset your project schedule and your budget.
Our advice: anticipate the tests! And carry out the pre-qualification tests when you have a product the closest possible to your desired final one.
>> Learn more about certifications with this article.
There is nothing to worry about!
The main thing is to realise that industrialisation is complex, and therefore to anticipate as much as possible.
Put like that, it may sound like theory. And yet, adopting this “anticipatory” mindset is the best advice we can give you.
That’s exactly what In&Motion did when approaching their connected airbag project. Here is their testimonial:
When thinking about the industrialisation of your intelligent product, one of the tips to follow is to separate the functional aspect. This objective is often achieved after a PoC (Proof of Concept) or a first prototype.
And the second step, evaluate the effort and the tools to be put in place in order to be able to produce and market the product.
There is still a long way to go after having validated the product architecture thanks to the PoC (Proof of Concept) before moving onto the industrialisation of the finished product. Numerous tests and iterations are essential to guarantee the reliability of the finished product.
Make an appointment to discuss my industrialisation
The main stages in the industrialisation of its product
Industrialisation is anticipated well in advance. There are many development phases to go through before reaching manufacturing and then marketing. The question you ask yourself is: “Where do I start?”
1. Define each dimension of the product beforehand/in advance to prepare its development
It should be noted that the optimal development of a product always involves several iterations. The first prototype will allow errors and nonconformities to be checked and corrected, in order to produce a second version that is more complete than the first until the desired result is obtained.
What is the target market?
Before you start marketing your product, you need to determine your target markets. If you plan to sell your product abroad, you will have to anticipate the certifications and standards required. Certain standards often require a variation and prerequisites to be integrated into the design of the product.
What volumes?
Similarly, you need to determine the volumes that may be available, as well as the use that will be made of your product.
Selecting partners
You will have two types of partners: subcontractors and distributors.
The distributor(s) will offer you the components for your electronic board. They will inform you about the durability of the components, their cost and their availability. They highlight existing technical solutions and can direct you towards alternative solutions that are more durable and easier to provision in the future. It is therefore essential to maintain good relations with your distributors.
The subcontractor(s) will assemble the components to produce your electronic board. They will manufacture the few units at the start and carry out the tests afterwards. They do not intervene until the final phase of development.
2. The different stages of development
The PoC (Proof of Concept)
To begin with, it is often customary to carry out an initial PoC, very often through the assembly of sub-assemblies (development kits, component evaluation kits, etc.). However at this stage, there is no search for integration or optimisation. The objective is simply functional: to demonstrate the feasibility of the product and not, for the moment, its possibilities for industrialisation or even prototyping. It is from this first PoC that it is then possible to design rapid prototypes in small quantities. To do this, specifications must be drawn up based on the initial results of the PoC tests.
The first prototype
With this design diagram of your first electronic board to be prototyped, you must approach the distributors, who will offer you their technical solutions (components), and their integration into the design of your board. You then obtain the V1 prototype.
The V2 prototype or final validation prototype
This first prototype will enable you to highlight certain errors and thus correct nonconformities in order to launch the V2 phase of the prototype. Ihis way, and depending on the number of iterations desired or possible, you will give your product a certain reliability to launch comfortably into industrialisation.
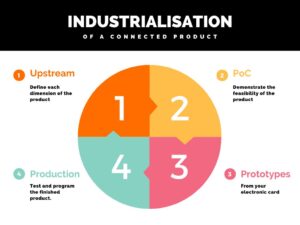
This iterative part also allows you to test and validate the overall functionality of the board. And it is
from this point that you will need to work with a subcontractor for the mass production of the cards, and thus integrate the first constraints linked to its production tools.
When all these stages are validated, industrialisation can begin.
3. Industrialisation of the connected object
The development stages have defined the finished product to start the production phase. The means and tests of post-production are to be determined in the industrialisation stage. This is the stage that will allow the reliability of the finished product to be tested and verified.
The tests
Firstly, all the necessary elements are integrated to test the board at the end of the production line. It will be important to carry out test benches and programming. During this stage, the approach with the EMS (the subcontractor) is essential for the integration of the constraints linked to its production tools.
Note: The development of one or more versions is possible. Nevertheless, this stage is more time-consuming than the prototype phase due to the size of the volumes and the financial impact.
Integration
Secondly, the stage of integration of the electronic board into the final product housing requires the same testing process. Mechanical integration, integration testing, packaging as well as shipping are the next steps to be taken into account in the industrialisation of connected objects.
Final assembly
The third step is to subcontract the final assembly. Your design office will act as an intermediary between the subcontractors and the manufacturers/distributors for the set-up of the production line and the final integration test. It is the guarantor of the collaboration and quality of manufacturing and assembly.
It is then possible to launch a first pre-production of the assembled product. This has the advantage of detecting any remaining problems. A few samples of this stabilised pre-series are then taken for qualification testing. This allows the necessary certifications to be obtained before the product is put on the market.
Certifications
Is the file finalised? You will have to look into certifications (NF, CE, etc.). You should know that in Europe, you can self-certify a product. However, this involves very specific and expensive equipment. Nevertheless, you can turn to expert laboratories.
In order to be able to apply the communications standards (Bluetooth, Wifi, etc.) to the final product, it is also necessary to register the product with organisations that oversee these protocols. For example, Bluetooth standards are supervised by the SIG. This stage involves anticipating the purchase and registration of licences with the consortia. On average, this represents a cost of 4000 euros per year.
At the end of all these stages and if the application is positive, your design office tells the manufacturer to launch production. This last stage involves anticipating the supply of components.
Industrialization of connected products with Rtone
Rtone is a consultancy specialising in the IoT pathway.
Rtone is a team of experts in the design, industrialization and operation of your connected objects. We have extensive experience with the various stages and difficulties inherent in the production process.
Whether you have a small or large series project. In this way, we can make you aware of phases that you may have underestimated.
We have also established strong partnerships with distributors and manufacturers. This is all the more important as each project is different and involves a specific integrator.
To make the best choice of integrator, we first carry out an audit to evaluate the production resources. We then set up a comparison of manufacturers in order to propose the most suitable ones matching our clients’ needs.
“As a result, the industrialisation of your connected object takes the best route: step by step until production.
Whether you choose to carry out a production “made in France”, in Europe or on another continent.
Would you like to talk to us about your project?
Let's make an appointment together